Implantable Device Coating and Membrane Development
Application of a coated membrane or covering to an implantable device offers several functional benefits. The most popular reason is to create a blood impermeable barrier, occluding blood flow to desired locations or creating an impermeable seal. A membrane may also inhibit ingrowth of a tumour or tissue, while enabling subsequent removal of the device, if needed. The application of porous holes to the membrane, in turn creates a filter design that can be used for embolic protection or as part of a retrieval devices.
These coverings can be extremely low profile, facilitating delivery to tortuous or distal anatomy, but also durable, overcoming stresses associated with a wide variety of implant designs, whether braided, laser cut frames, or fabrics. The choices for an elastomeric covering, such as silicones, polyurethanes and co-polymers, should be based on the following key selection criteria.
Things to consider when thinking about, or selecting an implant coating:
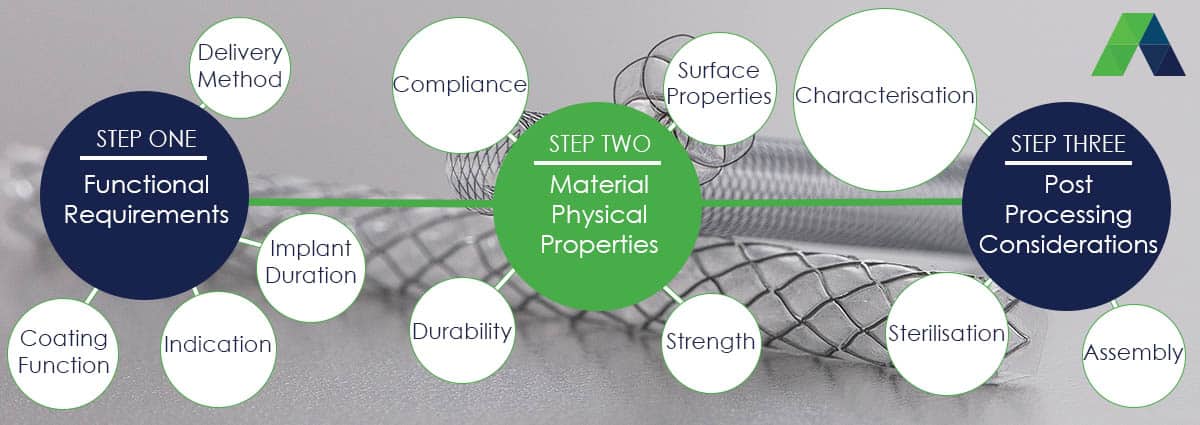
1. What is the function of the device being coated?
- Is it an occluder, retrieval device, stent, textile fabric or mesh?
2. Where will the device be placed?
- What types of tissue or fluids will it come into contact with?
- e.g. stomach acid, high or low pressure blood flow, areas at risk of infection.
3. What is the intended life expectancy of the device?
- Will it be implantable or non-implantable?
- Will it be implanted for greater than 29 days?
- Does it need to be resorbable, and if so what is the degradation profile?
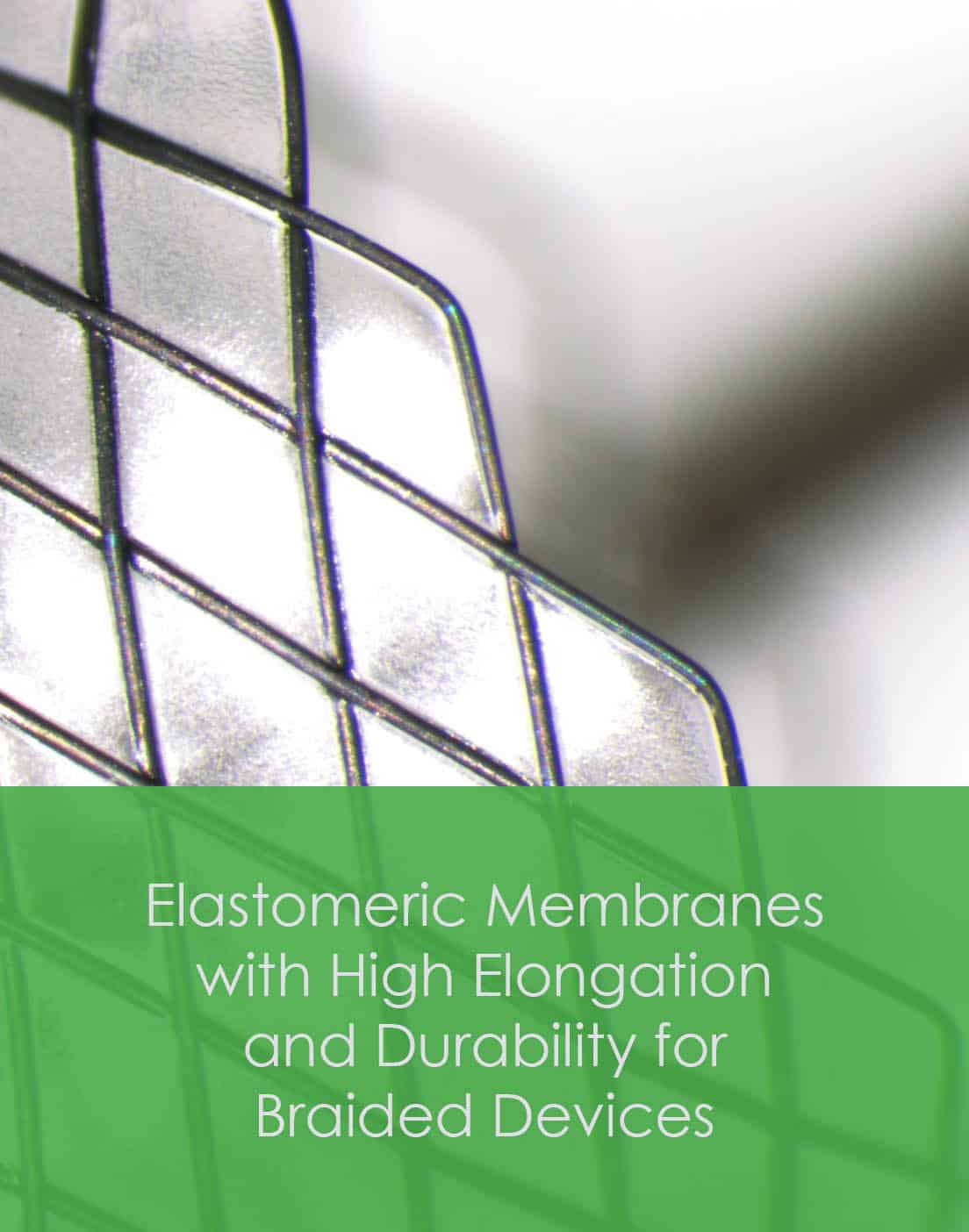
4. How will the device be delivered or placed?
- Does it require transcatheter delivery?
- If so, what is the crimp profile and effective thickness limitations on the covering that ensure deliverability? Is there anything in the crimping process that could damage the coating?
- Are there significant forces required to crimp and maintain the implant at a low profile? i.e. will it need a low coefficient of friction?
- Will the device be deployed and retrieved multiple times? i.e. how abrasive resistant does it need to be?
- Does the implant need to be sutured in place?
- What is the expansion profile of the implant, going from crimped to deployed, and vice versa?
5. How will the membrane affect the performance of the frame and vice versa?
- Will the frame design allow for or impede coating application?
Many companies focus their attention on the frame design, before considering the effect of the coating or membrane to be applied. It is important that the effect of the membrane is considered as early as possible in the frame design.
Remember that the frame design should accommodate the membrane, providing space for the material once crimped. The membrane may act as a passive layer on the implant or may impart specific mechanical characteristics. In the latter case, it may be possible to reduce the amount of material, wire or struts used in the frame, where the coating material influences the mechanical characteristics sought.
6. What are the surface properties of the substrate of frame to be coated?
- Is the surface optimised for coating?
- Will it be electropolished or not?
- Are there sharp edges or points in the design that could pierce the material?
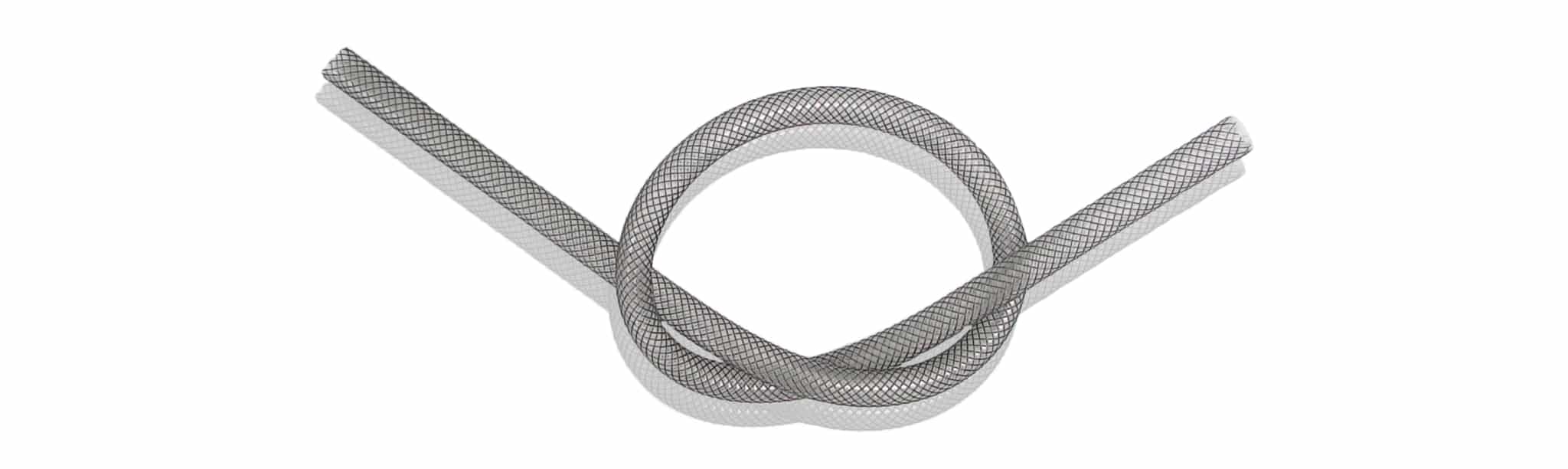
7. All of the above questions indicate the performance traits necessary for the covering, which translate to a range of physical properties for the material, such as:
- High ultimate elongation
- High ultimate tensile strength
- High tear strength
- Specific shore hardness
- Abrasion resistance
- Solvent/chemical resistance
- Biocompatibility (preventing thrombogenicity)
- Tacky/ non-tacky or lubriciousness surface qualities
- Anti-fouling or antimicrobial properties
Before making final selection of the material to be used on the membrane it is important to consider post processing implications.
8. At what step in the manufacturing process will the coating be applied:
- Will post processing steps such as device assembly, damage the membrane.
- What measures are needed to protect the device and minimise handling.
- Can the device be coated as a final step?
9. What characterisation is required for the covering?
- Adhesion of the covering to the substrate?
- Direct, non-contact thickness characterisation?
- Permeability/ Leak testing
10. What are the likely packaging or sterilisation requirements?
- Will it require any special packaging to prevent damage?
- If the coating is resorbable, has the appropriate packaging been considered?
- What sterilisation cycle is intended for the device?
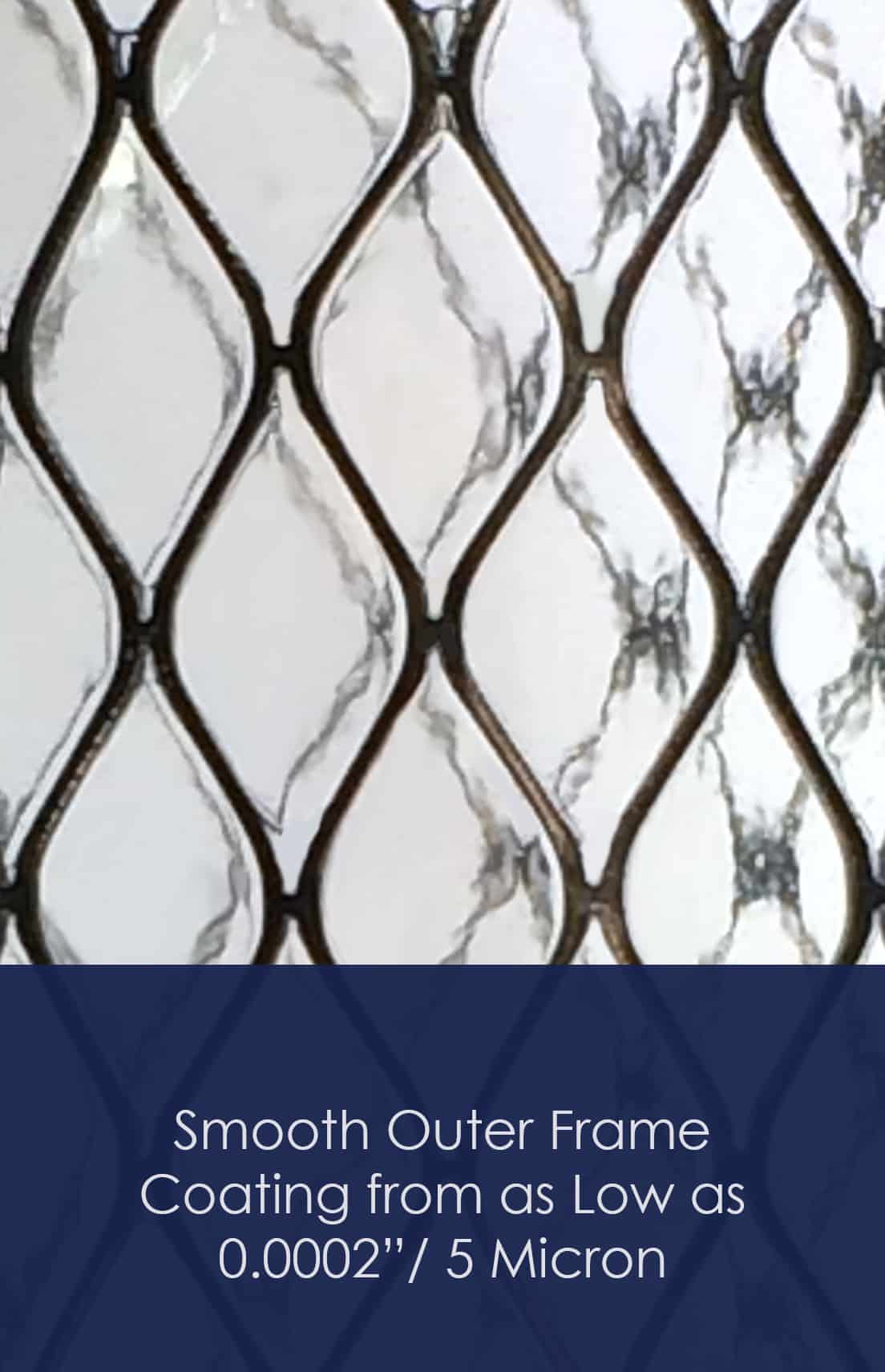